Wolf PVG trusts in meltblown technology from Oerlikon Nonwoven
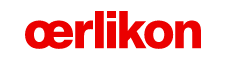

Markus Seele, COO Wolf PVG, and Andreas Schnell, Head of Nonwoven Production Wolf PVG, trust in the meltblown technology from Oerlikon Nonwoven.
Neumünster, 4th February 2021 – Oerlikon Nonwoven has successfully commissioned a double-beam meltblown plant with ecuTEC+ electro charging unit at Wolf PVG GmbH & Co. KG. With this plant, the East Westphalian company can now provide nonwovens for the production of surgical and FFP2 masks. In addition to this filter material, which is in great demand today, high-quality meltblown nonwovens can also be produced for medical and industrial filter applications. The plant has now been running for several weeks under stable production conditions with optimal nonwoven fabric quality of the highest standards.
With the beginning of the corona pandemic and the shortage of protective masks that ensued, Wolf PVG GmbH & Co. KG, a wholly-owned subsidiary of the Melitta Group, switched part of its production capacities to nonwoven mask fabric production. As a highly specialised system supplier for everything to do with vacuum cleaners and industrial filter technology, the company from East Westphalia can fall back on its extensive know-how and many years of experience.
With the meltblown plant from Oerlikon Nonwoven, Wolf PVG is further expanding its production capacities. The plant, with its two beams and the ecuTEC+ electro charging unit, is optimally designed for the production of face mask material. The plant is also ideal for the production of other filtration nonwovens. “A decisive point for investing in a plant from Oerlikon Nonwoven was the flexibility of the plant in relation to the possible product portfolio and the competence of the manufacturer,” explains Markus Seele, COO of Wolf PVG. And Dr. Ingo Mählmann, Senior Vice President Sales & Marketing Oerlikon Nonwoven, adds: “Thanks to the numerous setting options for the electrostatic charge provided by the ecuTEC+, the optimum loading status can be set depending on the filter application.”

Oerlikon Nonwoven double-beam meltblown system – here with integrated ecuTEC+ for electrostatically-charging the filter media.
ecuTEC+ electro charging unit from Oerlikon Nonwoven complements filter nonwoven plants
The meltblown technology from Oerlikon Nonwoven is considered the most technically efficient process for the production of highly effective filter media from plastic fibres. The ecuTEC+ electro charging unit also makes a significant contribution to this. With the patented process, spunbond and meltblown materials can be charged electrostatically and thus the filter performance can be significantly increased. In this way even the smallest particles are safely filtered. Nonwoven manufacturers are thereby largely free to choose and can set the optimal charging method and intensity for their filter application.
About Oerlikon
Oerlikon (SIX: OERL) engineers materials, equipment and surfaces and provides expert services to enable customers to have high-performance products and systems with extended lifespans. Drawing on its key technological competencies and strong financial foundation, the Group is sustaining midterm growth by addressing attractive growth markets, securing structural growth and expanding through targeted mergers and acquisitions. A leading global technology and engineering Group, Oerlikon operates its business in two Divisions – Surface Solutions and Manmade Fibers – and has a global footprint of around 11 000 employees at 182 locations in 37 countries. In 2019, Oerlikon generated CHF 2.6 billion in sales and invested more than CHF 120 million in R&D.
For further information: www.oerlikon.com
About the Oerlikon Manmade Fibers division
With its Oerlikon Barmag, Oerlikon Neumag and Oerlikon Nonwoven brands, the Oerlikon Manmade Fibers division is one of the leading providers of manmade fiber filament spinning systems, texturing machines, BCF systems, staple fiber systems and solutions for the production of nonwovens and – as a service provider – offers engineering solutions for the entire textile value added chain.
As a future-oriented company, the research and development at this division of the Oerlikon Group is driven by energy-efficiency and sustainable technologies (e-save). With its range of polycondensation and extrusion systems and their key components, the company caters to the entire manufacturing process – from the monomer all the way through to the textured yarn. The product portfolio is rounded off with automation and Industrie 4.0 solutions.
The primary markets for the product portfolio of Oerlikon Barmag are in Asia, especially in China, India and Turkey, and – for those of Oerlikon Neumag and Oerlikon Nonwoven – in the USA, Asia, Turkey and Europe. Worldwide, the division – with more than 3,000 employees – has a presence in 120 countries with production, sales and distribution and service organizations. At the R&D centers in Remscheid, Neumünster (Germany) and Suzhou (China), highly-qualified engineers, technologists and technicians develop innovative and technologically-leading products for tomorrow’s world.
For further information: www.oerlikon.com/manmade-fibers