Oerlikon Nonwoven presents portfolio at the FILTECH 2023
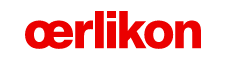

The hycuTEC process easily achieves filtration efficiencies in excess of 99.99% in the case of typical filter media.
Sustainable system solutions for filtration requirements
Neumünster, December 1, 2022 – sustainability, quality and efficiency are today’s requirements for systems solutions for filtration applications and their end products. These requirements are covered by the Oerlikon Nonwoven product portfolio in every respect. The company will be showcasing its meltblown and spunbond portfolio at the upcoming FILTECH in Cologne between February 14 and 16, 2023. Trade fair visitors will be able to meet the team at Stand B18 in Hall 8 to find out more about the hycuTEC charging unit, this year’s FILTREX Innovation Award winner, among other things.
hycuTEC – technological quantum leap for filter media
In the case of its hycuTEC hydro-charging solution, Oerlikon Nonwoven offers a new technology for charging nonwovens that increases filter efficiency to more than 99.99%. For meltblown nonwovens producers, this can mean material savings of 30% with significantly superior filter performance. Due to its extremely low water and energy consumption, the hycuTEC is also a future-proof, sustainable technology, as the process can be used without any additional drying steps in the case of most applications.
Sustainable nonwovens made from bio-based polymers
The bio-based polymer PLA (polylactic acid) is the perfect alternative for those wanting to manufacture sustainable nonwovens. And the Oerlikon Nonwoven meltblown and spunbond technologies are ideally suited for processing PLA, for example. To visualize this, the Neumünster-based systems builder will be presenting medical oronasal masks made from PLA at the FILTECH, whose protective effectiveness and wear comfort are equivalent to those of conventional PP masks.
Spunbond solutions for filter applications
Spunbond products are becoming increasingly important in filtration applications – as backing materials for filter media and as the filter media themselves. The fact that the nonwoven structure can be tailored to specific tasks enables targeted, customer-specific requirements for various functions to be realized. And combining various functions in a single layer is also possible.
The bi-component spinning process enables the creation of completely new nonwoven structures and hence the incorporation of various functions in a single material. The bicomponent spinning process permits various fiber cross-sections, while standard virgin polymers, bio-based polymers and recycled polyester can be used as raw materials.
About Oerlikon
Oerlikon (SIX: OERL) is a global innovation powerhouse for surface engineering, polymer processing and additive manufacturing. Its solutions and comprehensive services, together with its advanced materials, improve and optimize the performance, function, design and sustainability of its customers’ products and manufacturing processes in key industries. Oerlikon has been a technology pioneer for decades. All developments and activities have their origins in the passion for supporting customers in achieving their objectives and increasing sustainability. Headquartered in Pfäffikon, Switzerland, the group has two divisions: Surface Solutions and Polymer Processing Solutions. The group has a global footprint of more than 11,800 employees at 207 locations in 38 countries and generated sales of CHF 2.65 billion in 2021.
For further information: www.oerlikon.com
About the Oerlikon Polymer Processing Solutions division
With its Oerlikon Barmag, Oerlikon Neumag, Oerlikon Nonwoven and Oerlikon HRSflow brands, the Oerlikon Polymer Processing division focuses on manmade fibers plant engineering and flow control equipment solutions. Oerlikon is one of the leading providers of manmade fiber filament spinning systems, texturing machines, BCF systems, staple fiber systems and solutions for the production of nonwovens and – as a service provider – offers engineering solutions for the entire textile value added chain. Furthermore, Oerlikon offers a range of a high-precision flow control solutions. This currently includes a large selection of gear metering pumps for the textile and other sectors such as automobile construction, the chemical industry and the dyes and lacquers industry. With Oerlikon HRSflow, the division develops innovative hot runner systems for the polymer processing industry. In collaboration with Oerlikon Balzers, it offers highly-efficient, effective coating solutions from a single source.
As a future-oriented company, the research and development at this division of the Oerlikon Group is driven by energy efficiency and sustainable technologies (e-save). With its range of polycondensation and extrusion systems and their key components, the company caters to the entire manufacturing process – from the monomer all the way through to the textured yarn and other innovative polymer materials and applications. The product portfolio is rounded off with automation and Industrie 4.0 solutions.
The primary markets for the product portfolio of Oerlikon Barmag are in Asia, especially in China, India and Turkey, and – for those of Oerlikon Neumag and Oerlikon Nonwoven – in the USA, Asia, Turkey and Europe. Oerlikon HRSflow is, above all, active in the key automotive markets. These include Germany, China, Korea and Brazil. Worldwide, the division – with more than 4,500 employees – has a presence in 120 countries with production, sales and distribution and service organizations. At the research and development centers in Remscheid, Neumünster (both Germany), San Polo di Piave / Treviso (Italy) and Suzhou (China), highly-qualified engineers, technologists and technicians develop innovative and technologically-leading products for tomorrow’s world.
For further information: www.oerlikon.com/polymer-processing