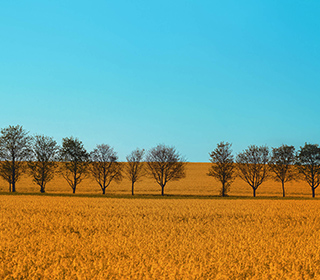
Beckmann Converting
Beckmann Converting is taking sustainability to the next level. Their ultrasonic laminating process only uses the raw materials of the composite to form the bonding links at the laminate weld points.
Freudenberg Performance Materials began recycling plastic bottles more than 30 years ago. The bottles are sorted, cleaned, and crushed into flakes that are then melted and spun into a continuous yarn which is made into nonwoven materials.
A large share of the 2.5 billion PET bottles that Freudenberg Performance Materials recycles annually at its plants in Novedrate and Pisticci, Italy; and in Colmar, France finds new life in many specially developed products.
Freudenberg Performance Materials recycles polyester for carpet tile backing materials and carpet floors to dampen noise. Bottle material can even be found in the doormats used at the entrances to buildings, among other areas. For the construction sector, Freudenberg experts transform the recycled PET into nonwovens used in noise and heat insulation. So-called bitumen membranes in turn are used on roofs. They waterproof and reinforce roof surfaces, so moisture has no opportunity to penetrate them.
We manufacture and sell more than 250 different products for the garment industry using recycled polyester as a raw material at our interlining and thermal insulation manufacturing sites in around the globe. Shifting to the use of recycled polyester fibers has saved the equivalent of at least 228 million bottles over the past 5 years alone from going to waste.
Reduced Footprint:
Using recycled fibers has a dual benefit; they create a new use for what would otherwise be single-use disposed plastic bottles, and the manufacturing of recycled fibers has a lower environmental footprint as compared to virgin polyester fibers. Research shows that producing fibers from recycled post-consumer waste requires 75% less water, 47% less energy, and generates 55% fewer emissions than fibers made from the original petroleum-based raw material.