Biax-Fiberfilm expands meltblown fabric production
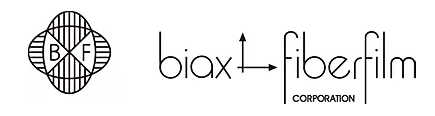
The struggle to meet the global demand for quality masks has many layers, starting with the rare material that the masks are made of, according to NPR. The melt-blown fabric is a “fine mesh of synthetic polymer fibers that forms the critical inner filtration layer of an N95 mask….” [Miami Herald, 4/17/2020]
Greenville, WI, April 24, 2020 – Biax-Fiberfilm Corporation of Greenville, WI, has announced expansion of its melt-blown fabric production for N95 masks and other medical applications. “We are currently running around the clock on two machines and the new capacity in Neenah will be five times higher,” says Biax-Fiberfilm President Douglas Brown. “The purchase of a former Kimberly-Clark facility in Neenah allows us additional space, plus some of the common machine parts (usually long lead time pieces) that will assist with our fast scale up. The plant will be a mix between old and new technology Developed by Biax-Fiberfilm”
The company expects its production startup at the new facility as early as June. With Brown’s patented technology and association with the world’s premier equipment supplier, Reifenhauser, the transition is expected to be a smooth one. Three 60-inch-wide production lines are planned. The nonwoven melt-blown fabric and a patented spun-blown system that produces fabrics that few others in the world can create are currently being produced at the headquarters Greenville factory. It is enough for about 3.5 million masks per day.
These complicated nonwovens fabrics consist of synthetic fibers stretched in an airstream and flattened into rolls for mask production. Exacting standards must be met, and quality controls are part of the process. “Our materials have been used in masks, physicians’ PPE and in the filtration industry,” says Brown. “A key is the breathable, yet tight ‘knit’ result that keeps out the virus.”
Mask manufacturers and medical products converters in Wisconsin are part of supply pipeline and further conversion into products. A recent industry call initiated by Masood Akhtar and Susan Stansbury of Cleantech Partners between healthcare converter-manufacturers, Governor Evers, Senator Baldwin associates and WEDC (WI Economic Development Corp.) has led to new potential collaborations in the state. According to John Michaud of American Custom Converting, Green Bay, a meeting between the companies is imminent.
According to Kirk Ryan, President and CEO of Little Rapids Corporation and its Graham Medical Division in Green Bay, “Many key materials come from overseas and I am happy to see innovation and investment happening in the Fox River Valley, particularly as we are expanding our facemask and PPE capabilities in Green Bay.”
________________________________________________________________________________________________
Douglas Brown has more than 28 years of experience with Biax-Fiberfilm. He is confident that with existing meltblowing and web/film stretching technologies combined with new ideas currently being developed “in our R&D Department on biodegradable microfibers and submicron fibers, Biax-Fiberfilm will remain an innovative leader.”